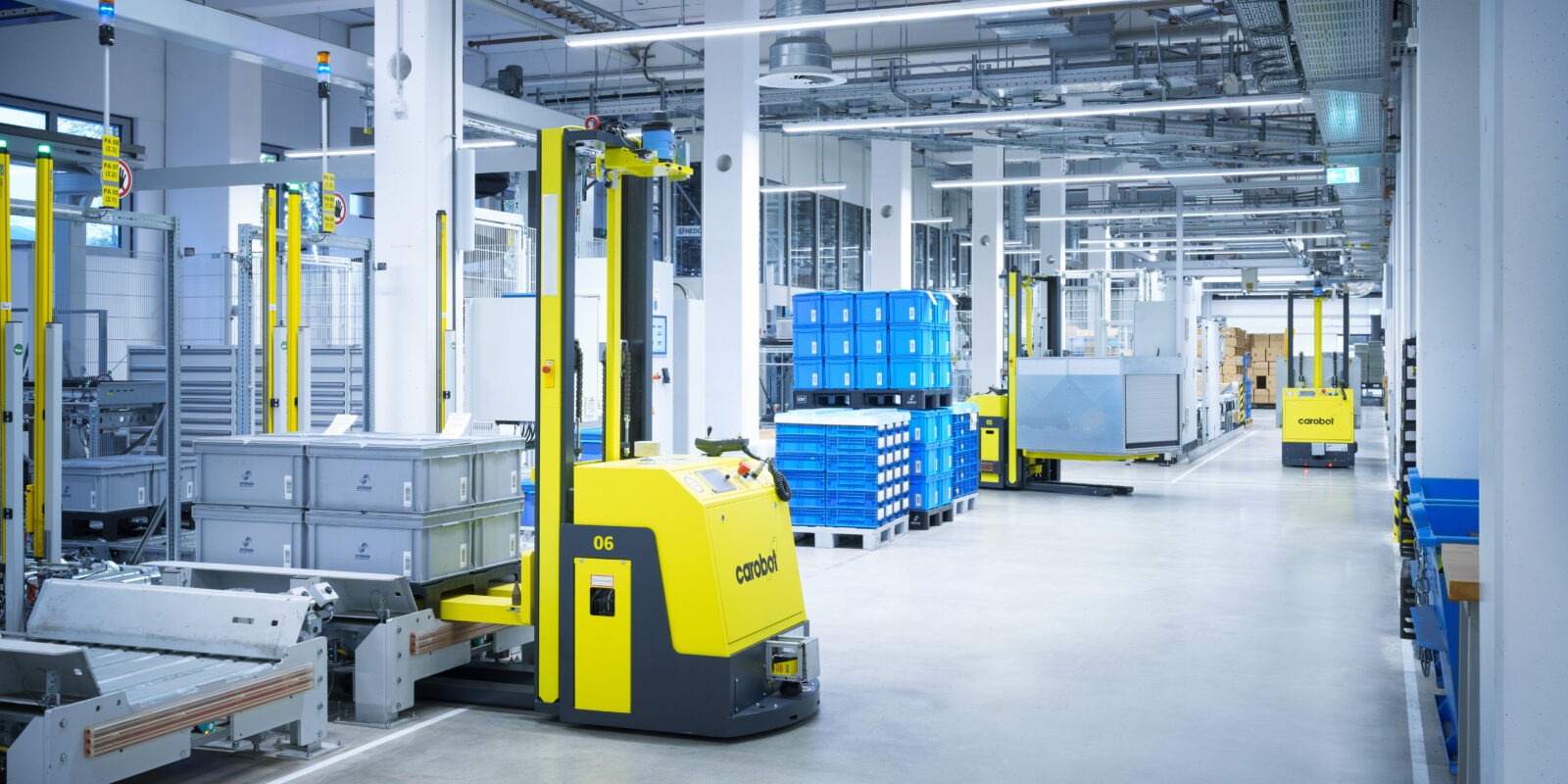
Stüken
Komplexe und flexible Produktionsversorgung
Das Unternehmen Hubert Stüken GmbH & Co. KG, kurz STÜKEN, mit rund 1200 Mitarbeitern gilt als weltweit führend im Bereich Tiefziehteile aus Metall. In Haushaltsgeräten und Armaturen, in Computern, Mobilfunkgeräten und Automobilen finden sich beispielsweise Produkte von STÜKEN.
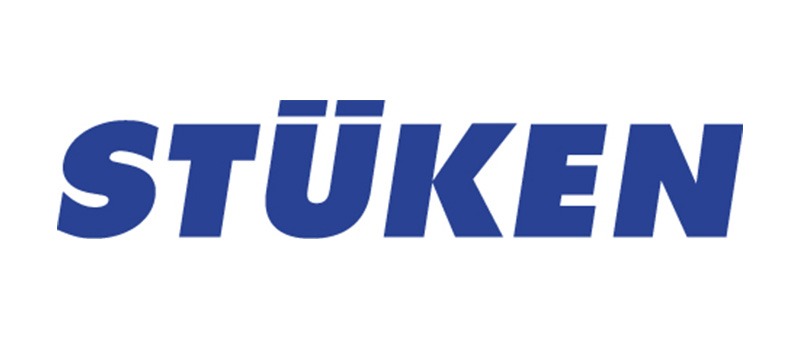
Kunde:
Hubert Stüken GmbH & Co. KG,
Rinteln | Deutschland
Systeme:
3-gassiges Multi Access Warehouse mit 21 ebenenwechselnden Shuttles und mittig angeordneten THM-Liften, eingassiges RBG-Lager für 200 kg schwere Behälter, 7 Fahrerlose Transportfahrzeuge, Fördertechnik an der Hallendecke, Palettierroboter
Die Präzisions-Tiefziehteile werden in großen Serien auf Stufenpressen und Stanzautomaten hergestellt und durchlaufen in der Produktion im Mittel zehn verschiedene Arbeitsgänge bis zum Fertigteil. Zwischen diesen Arbeitsgängen und vor dem Versand an die Kunden sind die Tiefziehteile im Werk zu transportieren sowie zu puffern.
Zur Optimierung der innerbetrieblichen Logistik wurden die nachgelagerten Bearbeitungsprozesse sowie die Anlieferung bzw. der Versand durch ein automatisches Kleinteilelager entkoppelt. Ein zusätzlicher Waschbehälterpuffer dient als weitere Schnittstelle zwischen der Produktion und dem logistischen Bereich. In diesem werden die Teile, die nach jedem Bearbeitungsgang gereinigt werden müssen, zwischengelagert.
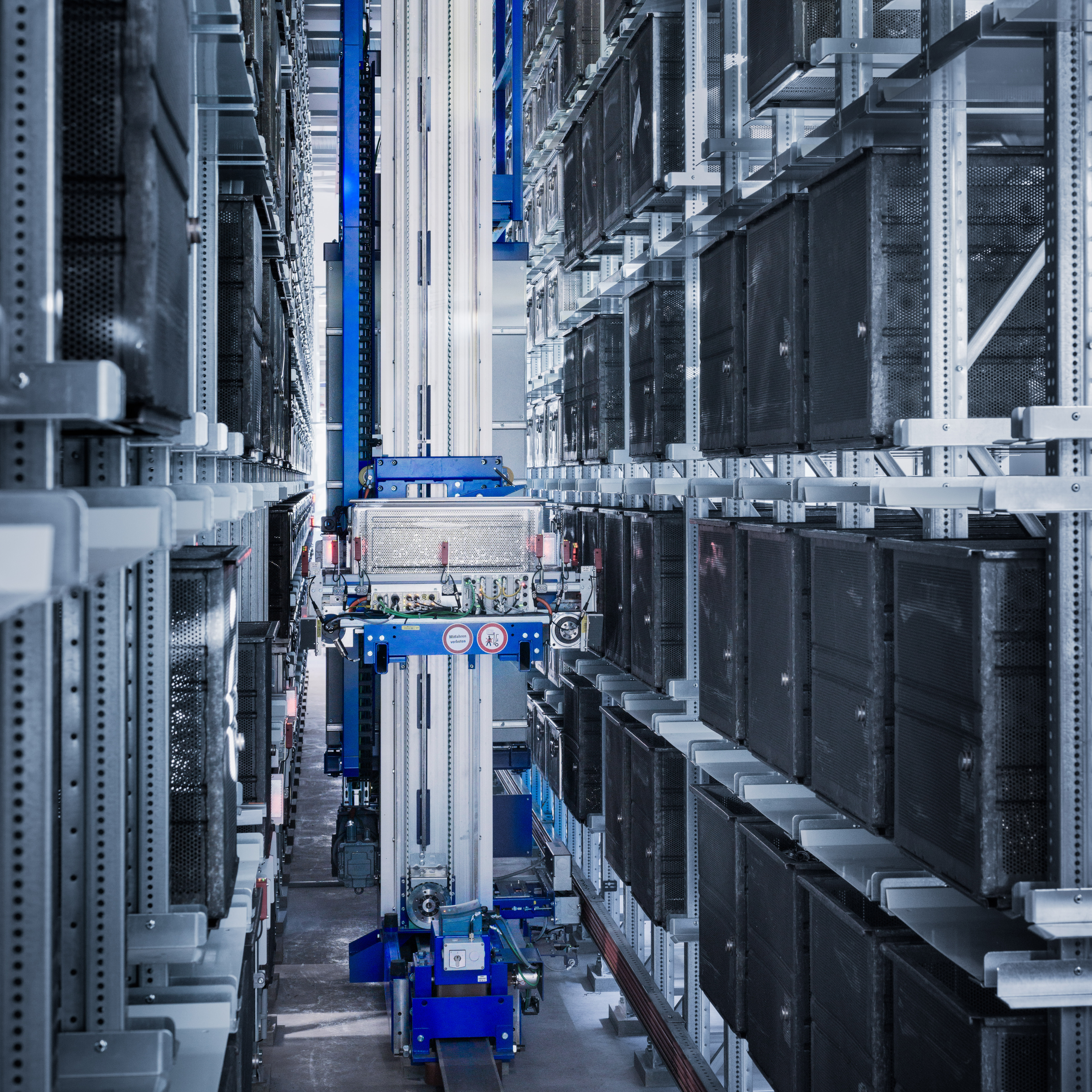
Es handelt sich um ein RBG-bedientes Lager inkl. Sequenzierfunktion für volle und leere Waschbehälter (bis zu 200 kg) aus und für die Produktion. Über das ebenfalls von psb gelieferte Fahrerlose Transportsystem (sieben Fahrzeuge) werden die Waschmaschinen, die Fertigungsschritte der Veredelung sowie das manuelle bzw. automatische Umschütten verknüpft. Diese automatisierten aber dennoch flexiblen Transportwege verringern die Logistikkosten, schaffen Raum für zukünftiges Wachstum und vereinfachen die technischen Prozesse.
Das nachgelagerte Multi Access Warehouse mit 75.000 Stellplätzen weist eine Besonderheit auf: Das 3-gassige Shuttle-Lager wurde auf einer Geschossdecke im Obergeschoss errichtet. Dank dieses Konzeptes fand die zentrale Lagervorzone ihren Platz unter der Decke der Logistikhalle. Damit konnte das Lager bzw. der komplette Logistikbereich auf sehr kleiner Fläche realisiert werden und die Verkehrswege auf dem Boden der Halle bleiben frei für die Gabelstapler und Fahrerlosen Transportsysteme, kurz FTS.
In dem Lager können die pro Gasse sieben Shuttle-Fahrzeuge die Lagerebenen über den Shuttle-Lift wechseln. Zwei Behälterlifte pro Gasse sind mittig ins Lager integriert und transportieren die Behälter von den Lagerebenen in die Lagervorzone und zurück. Die Lagervorzone ist direkt an den zentralen Verteilkreisel an der Decke im Erdgeschoss angeschlossen und damit an das automatische Palettieren/Depalettieren von Kartons und Kunststoffbehältern, das Etikettieren, das Kartonverschließen, den Qualitätssicherungsbereich sowie die Fehlerbearbeitung angebunden.
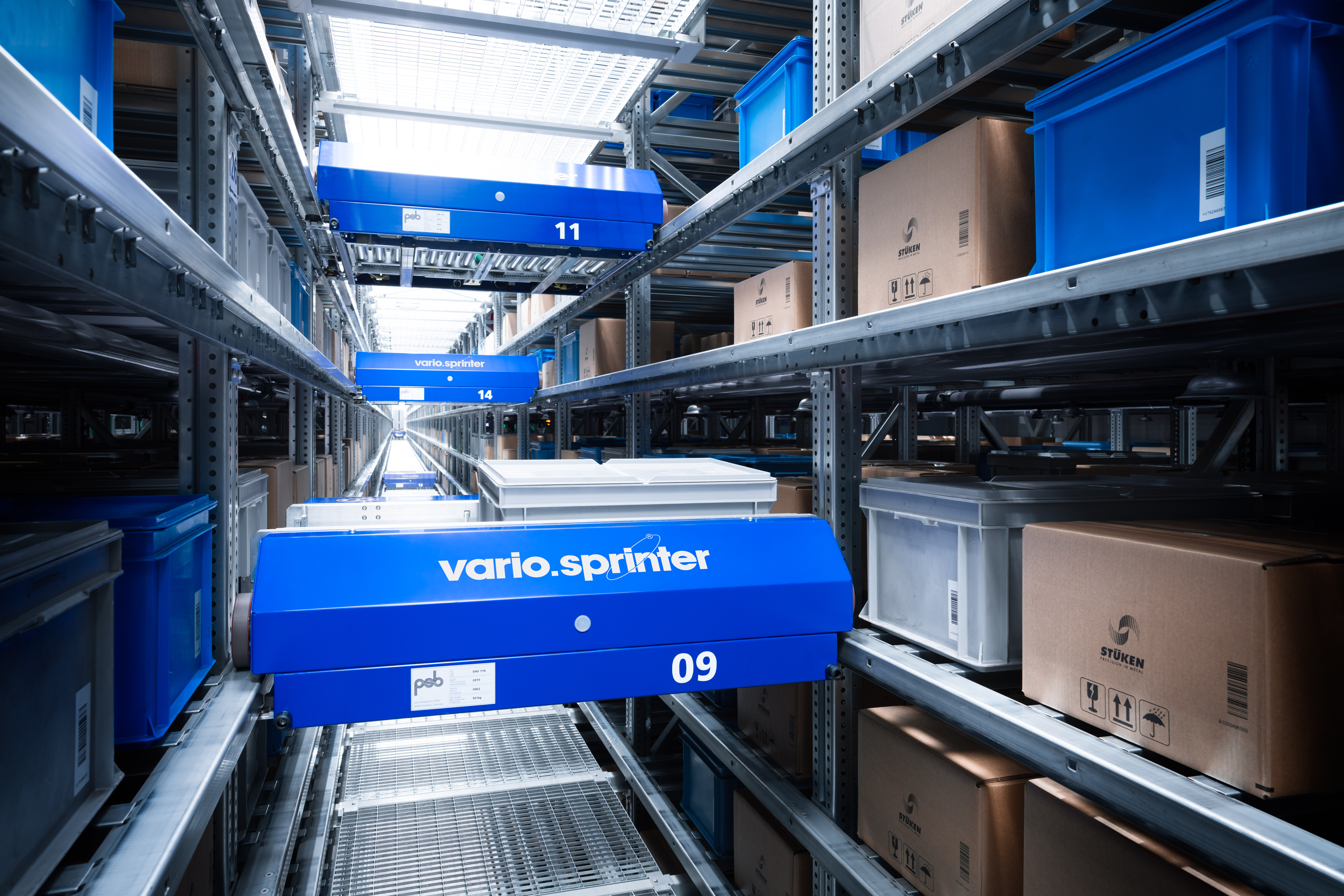
Für das automatische Palettieren/Depalettieren von Kartons und Kunststoffbehältern hat psb ein Flächenportal mit einem Roboterschlitten integriert. Die Ver- und Entsorgung dieses Bereichs mit Paletten erfolgt ebenfalls durch die FTS.
Galerie
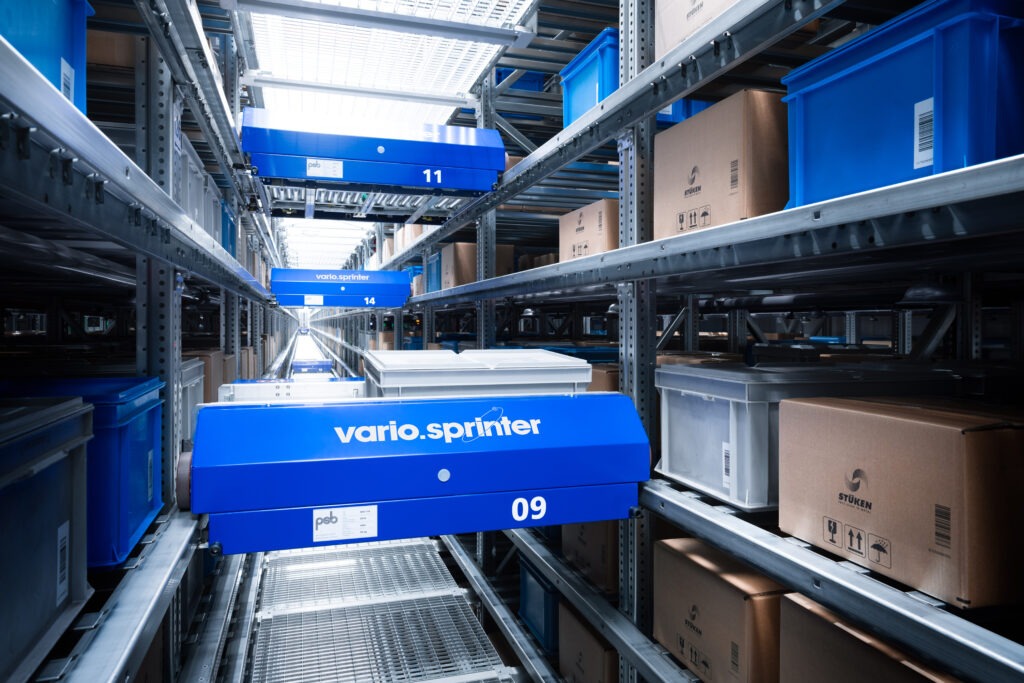
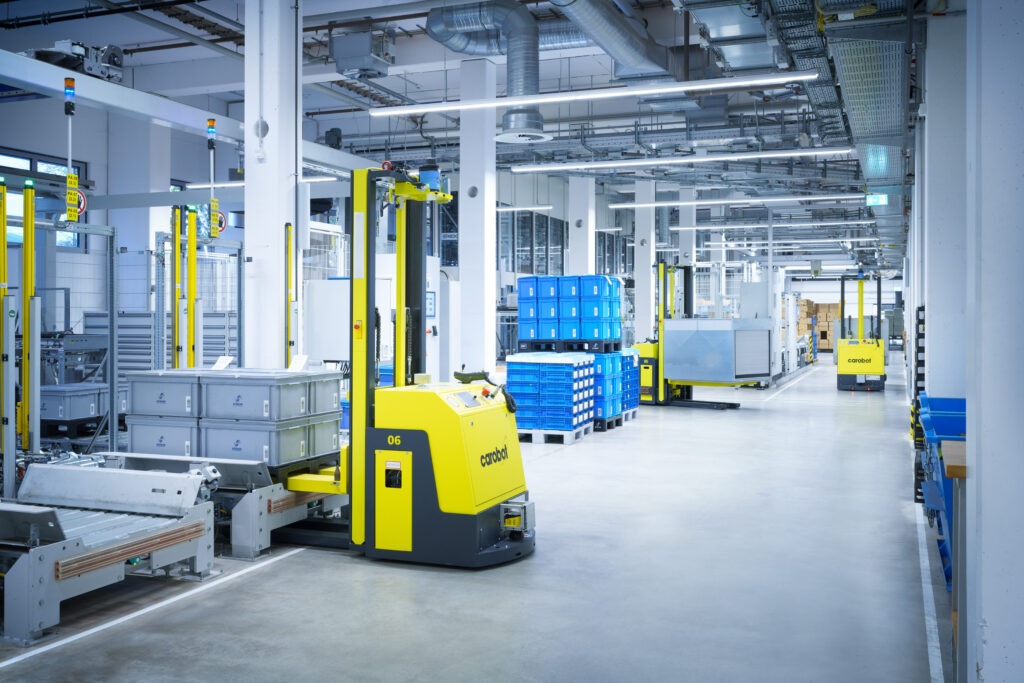
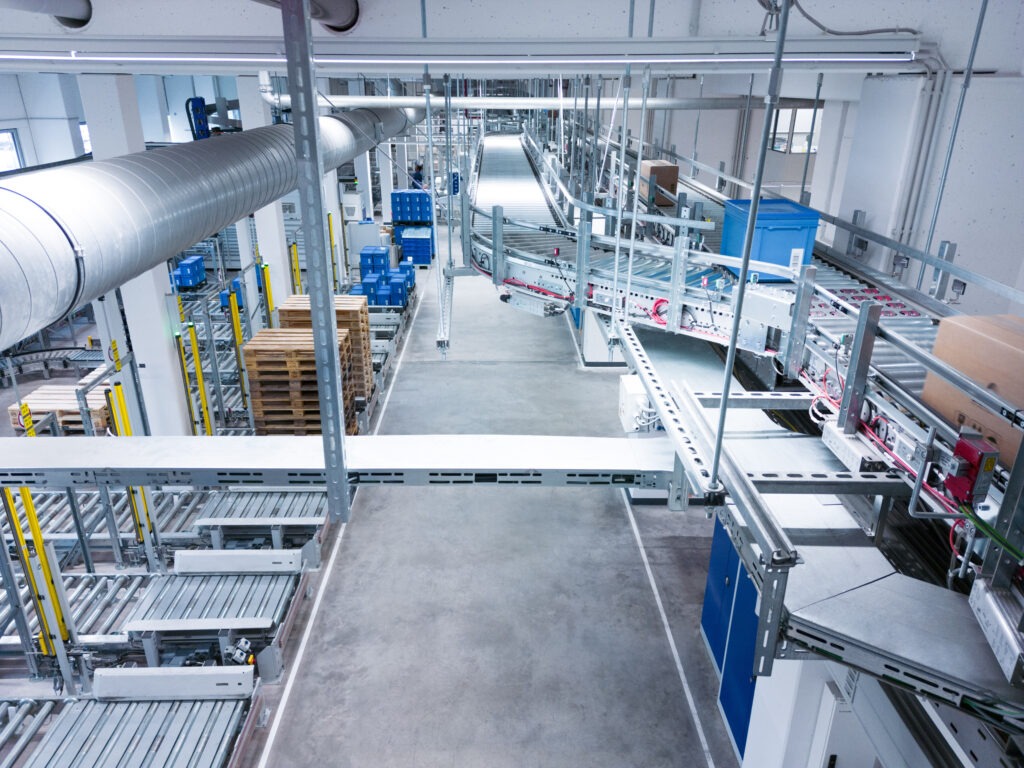
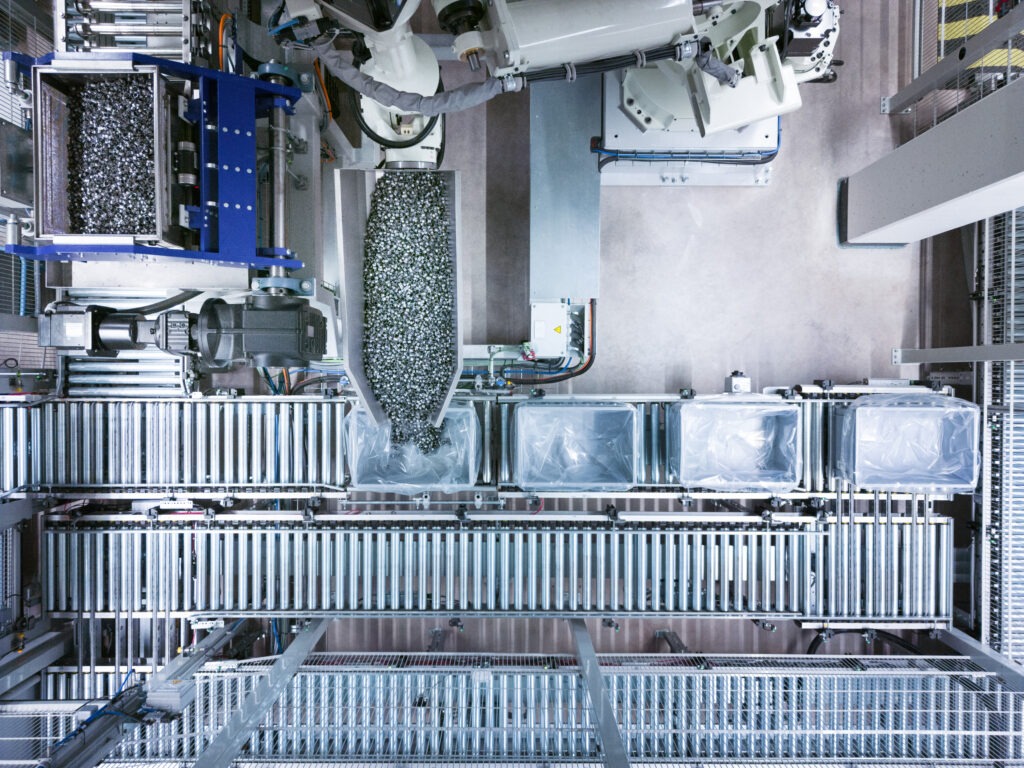
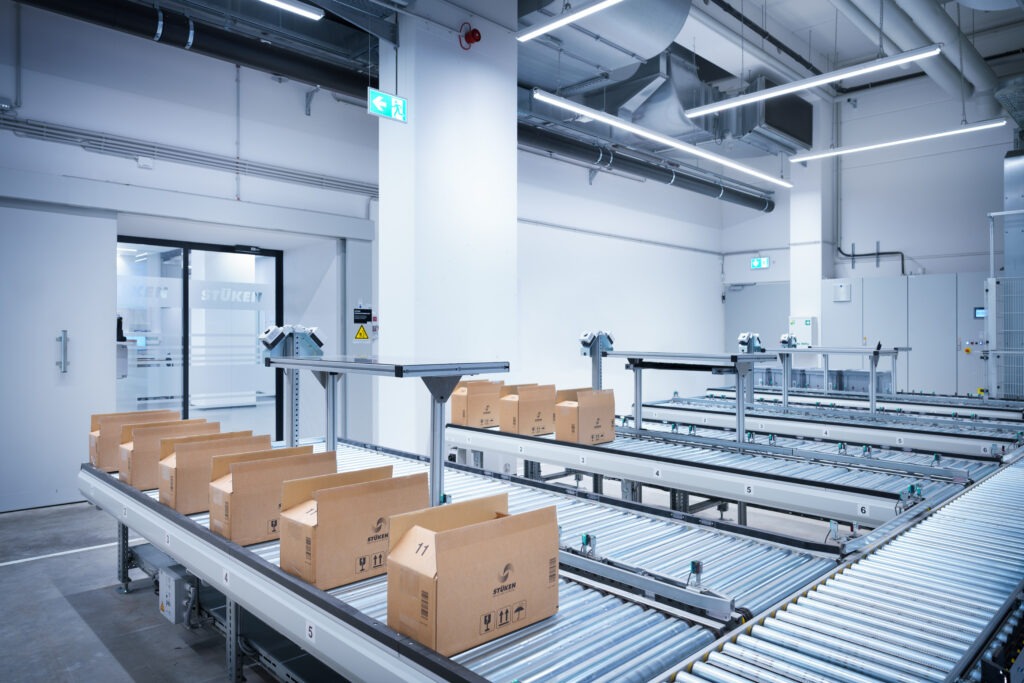
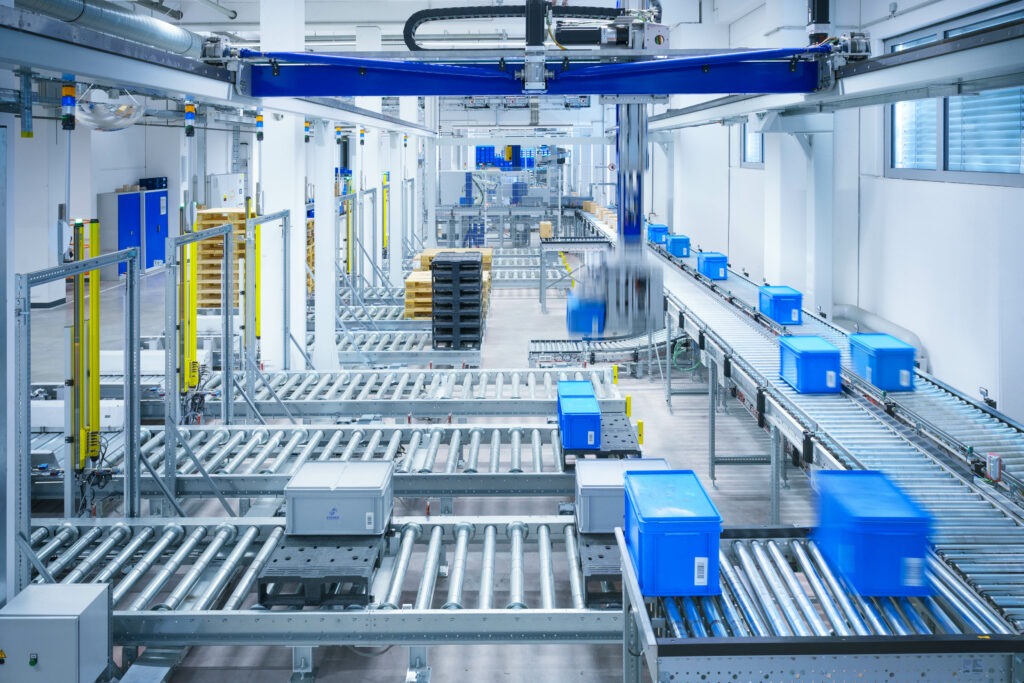